
4 trucs pour comparer le prix des résines
Il existe beaucoup de résines époxy sur le marché. Comment se retrouver parmi toutes ces formulations existantes ? Quelles caractéristiques techniques faut-il prendre en compte ? Que devez-vous comparer lorsque vous hésitez entre des résines de fournisseurs différents...
Quelle quantité de résine achetez-vous vraiment ?

Qu’est-ce qui pèse le plus lourd ? 1 kg de plumes ou 1 kg de plomb ?..
Il est bien clair qu’en valeur absolue, 1kg de plomb est bien égal à 1 kg de plumes.
Sauf que cette devinette aux allures désuètes fait intuitivement référence à une notion majeure en physique/chimie : la densité spécifique. Car, vous en conviendrez, il faut amasser beaucoup, beaucoup, beaucoup de plumes pour totaliser 1 kilogramme de plumes. En revanche, une petite quantité de plomb suffit à atteindre rapidement le kilo…
C’est la notion de densité spécifique qui permet de comprendre la quantité de produit, autrement dit le volume, que vous achetez réellement. En effet, qu’il s’agisse de couler des pièces, de fabriquer un moule, ou de surface à couvrir, c’est avant tout le nombre de litres dont vous avez besoin qui devrait vous aider à faire des comparaisons éclairées. Pas le format de contenant annoncé par le fabricant de résine ! Pas plus, le poids du kit que vous achetez… Quand on achète une résine, on devrait donc toujours se demander combien de litres de produits m’offre ce kit de résine.
Voilà pourquoi tout acheteur de résine doit savoir ce qu’est la densité spécifique !
1/ Qu’est que la densité spécifique

La densité spécifique est une notion de chimie importante. On parle aussi de gravité ou de masse volumique.
La masse volumique se définit comme la masse d’un matériau par unité de volume.
Quand on parle de densité spécifique d’un matériau, on prend l’eau comme mesure étalon 1 L = 1 Kg
Certains produits, comme les solvants, ont une densité spécifique basse variant de 0.65 kg/litre à 0.98 kg/litre. A l’inverse, certains matériaux ont une densité spécifique plus élevée comme par exemple l’aluminium, dont la densité spécifique est de 2,7 kg/litre.
2/ Pourquoi tenir compte de la densité spécifique pour acheter sa résine?
La notion de densité spécifique est importante pour déterminer la quantité / le volume de résine que vous achetez effectivement.
Cela s’avère d’autant plus utile si le prix est annoncé pour un format au kg. (Voir le cas d’étude #1)
De même, se fier à l’annonce d’un format gallon est parfois trompeuse. Certains fabricants font référence au gallon en tant que format de contenant, mais cela n’implique nullement qu’un volume de 1 gallon de résine, autrement dit 3.78 litres, est effectivement vendu dans ce contenant d’1 gallon.(Voir le cas d’étude #1)
En outre, plus la densité spécifique d’une résine sera importante, moins de volume de liquide sera nécessaire pour atteindre un poids donné. Si 2 résines sont vendues en kit de 20 kg par exemple. Vous aurez plus de quantité de résine avec un produit qui présente une densité plus faible. (Voir le cas d’étude #2)
Dans ces deux cas, il faut impérativement connaître la densité spécifique du produit pour savoir quelle quantité / volume/ nombre de litres de résine , on achète. Ainsi le volume réel, en litres de résine est donné par la formule suivante
POIDS EN KILOGRAMMES / DENSITÉ SPÉCIFIQUE = VOLUME EN LITRES
3 / Savez-vous vraiment combien de résine vous achetez et à quel prix ?
CAS D’ÉTUDE # 1 : QUI VEND RÉELLEMENT UN GALLON DE RÉSINE ?
2 manufacturiers, des résines aux caractéristiques identiques vendues sous des formats différents, l’un vend une résine en kilos , l’autre en litres.
NB: ce cas est purement fictif et ne sert que la cause de l’exercice et du calcul qui elle reflète bien des cas réels rencontrés
FABRICANT A
“Résine X100
Formats disponibles:
1 “Gallon Unit”/ 16 lbs/7.26 kg: 129 $
1 Gallon de partie A/ 1 Gallon de partie B
“FABRICANT B
“Résine Y100”
Formats disponibles:
Format 7.56 L : 139 $
3.78 Litres de partie A/ 3.78 Litres de partie B
5 Gallon Unité / 80 lbs/36.29 kg : 528 $
Format 37.8 L : 569 $
Densité spécifique : 1.04 g/cc
Dureté : 60 Shore A
Ratio : 1/1
Densité spécifique : 1.06 g/cc
Dureté : 60 Shore A
Ratio : 1/1
** normalement 1 gallon de résine = 3.78 litres de résine
Comment calculer la quantité de résine vendu par le FABRICANT A ?
Le FRBRICANT A vend sa résine polyuréthane X100 en format “gallon”, cela signifie qu’il vend un kit de 2 gallons , 1 gallon de A ( résine )et 1 Gallon de B ( durcisseur) (ratio 1/1) . Ce manufacturier annonce que son kit gallon de Résine X100 pèse 16 lbs/ 7.26 kg. On lit plus loin que le produit possède une densité spécifique (specific density) de 1.04.
Le FABRICANT B vend sa résine polyuréthane Y100en format 7.56 Litres, ce qui correspond à deux gallons de résines.
Ainsi, pour vérifier le nombre de litres effectivement vendus dans le kit gallon du FABRICANT A, vous devez utiliser la densité spécifique du produit pour trouver combien pèse 1 litre de produit.
Si la densité spécifique de produit est 1.04, cela signifie que 1 litre de la résine X100 pèse 1.04 kilogrammes (ou 1 CC = 1.04 grammes)
Finalement, pour savoir le nombre de litre qu’offre le kit du FABRICANT A, la formule de calcul est la suivante :
POIDS EN KILOGRAMMES / DENSITÉ SPÉCIFIQUE = VOLUME EN LITRES
Dans le cas de la résine X100 du FABRICANT A: la quantité en litre de résine est 7.26 kg /1.04 = 6.98 Litres
Par conséquent, ce manufacturier vend un kit Gallon qui contient seulement 6.98 Litres.
Qui vend le plus de résine ?
Quand le FABRICANT annonce vendre en gallon, il ne parle pas de la contenance de produit, mais bien du format du contenant ! Ce contenant pourrait effectivement contenir 1 gallon de résine, mais il ne le remplit qu’ à hauteur de 3.49 L au lieu de 3.78 L.
Donc, si l’on compare avec un FABRICANT B qui vend un format 7.56 Litres, soit un vrai 2 gallons plein de résines , soit 1 gallon de A et 1 gallon de B ( soit 2 x 3.78L) , le kit du manufacturier B est bien le plus généreux en quantité de résine.
4 / Savez-vous comparer le prix de deux résines ?
CAS D’ÉTUDE # 2 : QUELLE RÉSINE EST LA MOINS CHÈRE ?
Par ailleurs, pour faire une bonne comparaison de prix entre deux résines, on devrait toujours raisonner sur un prix au litre. C’est ce qu’illustre de façon plus frappante encore ce cas d’étude #2
2 FABRICANTS vendant un kit de résine en format 20 kg, avec deux densités spécifiques différentes.
Dans ce cas, on voit bien comment une différence importante de densité spécifique, se répercute sur la quantité de résine en litres effectivement vendues dans le kit. Au final, le calcul du coût au litre est sans appel. La résine du FABRICANT B est bien moins chère finalement !
5 / Que faut-il retenir ?
- Il faut se méfier des comparaisons basées sur une un prix qui mentionnerait des volumes de contenant. ; les fameux “kit gallons”
- Dès qu’un prix est annoncé en kg, il faut faire intervenir la densité spécifique pour calculer le volume de résine en litre
- La formule est la suivante : kg / densité spéc. = vol. en litres
En conclusion, l’acheteur de résine, comprend qu’une bonne comparaison de prix de résine, devrait se baser sur la quantité réellement vendue. Le meilleur comparatif est assurément le prix au litres. La vigilance des consommateurs est de mise quand les manufacturiers jouent sur l’ambiguïté des termes et vendent des kits en mettant l’accent sur le format du contenant et non sur la quantité réelle de produit vendue !
Résines epoxy, polyurethane, silicone : attention aux fausses bonnes idées
Vous travaillez avec une résine epoxy, polyurethane, silicone ? Attention aux fausses bonnes idées.
Il n’est pas toujours facile d’utiliser les résines thermodurcissables. Ce sont des produits techniques relativement exigeants. Nous nous efforçons toujours d’accompagner nos clients dans leur projet par un suivi personnalisé, mais il arrive que cela ne suffise pas. Nos experts du service technique sont parfois les témoins d’expériences malheureuses vécues par certains clients.
Voilà pourquoi quand on travaille la résine, c’est une mauvaise idée :
– d’être imprécis;
– d’improviser;
– d’être trop pressé
1. NON à l’ IMPRÉCISION
Pour être sûr que mon moule soit plus dur, j’ai encore ajouté de la partie B (durcisseur) à la résine

Pourquoi ce n’est pas une bonne idée ⇒
Tout d’abord, pour qu’une résine catalyse, c’est à dire que la réaction chimique de polymérisation opère correctement, il faut respecter un strict ratio. Illustrons ceci de façon schématique. Imaginons que notre partie A est constituée de molécules féminines et que la partie B se compose de molécules masculines. Si le ratio est de 1/1 (1 volume de A pour 1 volume de B), cela signifie que pour une polymérisation complète, c’est à dire pour que la réaction chimique s’opère de façon optimale, il faut un mariage / assemblage parfait de toutes les molécules féminines et masculines. (La chaîne moléculaire doit se refermer complètement )
Voilà pourquoi, on DOIT absolument effectuer des mesures précises sans quoi le risque est grand de ne pas obtenir de bons résultats
2.NON à L’IMPROVISATION
J’ai utilisé de la vaseline pour enduire mon moule et faciliter le démoulage
J’ai utilisé du PAM comme agent démoulant et tout a collé !
Pourquoi ce n’est pas une bonne idée ⇒ parce que, pour faciliter le démoulage, il faut utiliser spécifiquement un agent démoulant souvent à base de silicone, parfois à base de cire ou à base d’eau pour le béton.
J’ai ajouté de la litière à chat dans ma résine de moulage de polyuréthane et il a gonflé comme une balloune…
Pourquoi ce n’est pas une bonne idée ⇒ en incorporant la litière à chat, beaucoup d’humidité a été ajoutée au mélange.
En affaire, comme dans notre vie de consommateur, nous souhaitons tous faire des économies sur nos matières premières ou nos coûts de fabrication, mais lorsqu’on travaille avec la résine, improviser dans l’utilisation de produits inadaptés peut s’avérer désastreux et souvent beaucoup plus coûteux
3.NON à la PRÉCIPITATION
Pour accélérer le durcissement, j’ai placé mes moules dehors. Il fait – 5oC , ça devrait aider …
Pourquoi ce n’est pas une bonne idée ⇒ C’est tout l’inverse. La polymérisation est une réaction chimique qui produit de la chaleur quant les molécules de la partie A et de la Partie B réagissent ensemble. On parle d’exotherme. C’est pour cela que, plus on mélange de produit, plus le dégagement de chaleur est important, plus le temps de vie en pot est accéléré. Chaque résine a un temps de vie en pot différent. Vérifiez toujours que vous ne mélangez pas plus de produit que ce que vous êtes capable de travailler compte tenu du temps de pot qu’offre le produit.
Suivant la résine utilisée, il est parfois possible d’accélérer le temps de cure en chauffant le produit, mais ATTENTION, NOUS NE RECOMMANDONS JAMAIS DE BRÛLER LES ÉTAPES. Le phénomène de réticulation ou temps de séchage demande que la chaîne moléculaire soit totalement fermée, et ce, de la bonne façon. Tout processus extérieur va modifier cette chaîne et entraîner une perte, légère ou non, des spécifications…donc, dans le meilleur des mondes, la polymérisation à 22°C demeure la procédure idéale, amenant un résultat maximal.
Nous aimons souvent rappeler à nos clients que “l’on ne peut tirer sur une fleur pour la faire pousser plus vite !”
Voilà pourquoi nous encourageons systématiquement nos clients à tester au préalable la résine pour s’assurer qu’elle est bien compatible avec l’application. Il convient aussi de
tester nos produits pour valider les étapes et méthodes de travail.
Vous aussi avez connu de malheureuses expériences avec la résine, faites-nous en part en commentaires….
Pour des questions concernant l’utilisation de nos différentes résines, n’hésitez pas à communiquer info@dssfrance.fr
Comment éviter la formation des bulles dans la résine ?

Savez-vous comment éviter la formation des bulles dans une résine thermodurcissable? Plusieurs précautions peuvent être prises pour éviter la formation des bulles
En effet, plusieurs raisons peuvent expliquer la formation de bulles d’air à la surface de la résine, il s’agit donc de bien les comprendre pour ne pas favoriser le phénomène.
Pour prévenir la formation de bulles :
1. Attention au mélange !
En premier lieu, la formation de bulles provient souvent du mélange des parties A et B.
Voilà pourquoi, nous recommandons de tourner délicatement en suivant la forme du chiffre 8, sans sortir du récipient, en grattant bien le fond et les cotés du contenant jusqu’à ce que le mélange devienne homogène.
Éviter de tourner rapidement, soit manuellement ou mécaniquement, et ainsi former un vortex qui introduira une grande quantité d’air dans le mélange. Par la suite ces microscopiques bulles d’air feront leur apparition lors de l’exotherme du produit (la chaleur fera grossir les bulles qui remonteront à la surface).
Pour les petites quantités, il est toujours préférable de mélanger avec une spatule plate métallique d’environ un pouce de large. Il faut aussi éviter d’utiliser une spatule en bois. Le bois est une matière poreuse qui peut contenir de l’humidité et ainsi contaminer les résines polyuréthane et amener un dégagement de CO2 (dioxyde de carbone), c’est-à-dire, des bulles qui gonfleront et qui donnera l’impression d’une barre de chocolat Aéro.
Pour les plus grandes quantités, il est important de s’assurer d’utiliser un mélangeur de dimension appropriée. La tête du mélange doit toujours être plongée intégralement dans le mélange
Laisser reposer le mélange quelques instants, avant de couler, permet aux bulles de remonter naturellement à la surface.
Attention cependant, plus on attend, plus la résine épaissit *.
2. Sceller la surface à couvrir ou la matrice

Bulles formées par l’application d’une résine polyuréthane sur une planche de bois non scellée
L’apparition de bulles dans la résine peut provenir de la surface à recouvrir.
En effet, certains matériaux (bois, plâtre…) sont poreux ou contiennent de l’humidité ; cela peut favoriser la remontée de bulles d’air. La solution peut alors consister à appliquer une fine couche de résine qui servira de scellant. Cela se présente souvent avec des matrices.
Dans ce cas, pas besoin d’attendre que la couche soit totalement sèche pour couler votre époxy. Il est possible et même recommandé d’appliquer votre couche de résine alors que la couche de scellant demeure légèrement collante (on parle de “résine amoureuse”).
De même, si vous coulez votre résine dans un moule, veillez à ce que celui-ci soit parfaitement propre, exempt de poussières, ou de toute trace d’humidité ou résidus.
3. Autres paramètres à contrôler
Les autres éléments à prendre en considération vont dépendre de la résine avec laquelle vous travaillez
Environnement de travail
Certaines résines sont encore plus sensibles à l’humidité. C’est plus particulièrement le cas des polyuréthanes. Il faut donc veiller à travailler dans des environnements où l’humidité est contrôlée. Idéalement sous 60% d’humidité.
Viscosité de la résine
Plus une résine est liquide, plus elle se débulle facilement, car les bulles remontent plus vite à la surface.
A l’inverse, une résine possédant une plus grande viscosité laissera difficilement les bulles d’air s’échapper.
Épaisseur de la coulée de résine
De façon générale, il est plus aisé de débuller une couche mince de résine qu’une couche épaisse. Plus les bulles d’air doivent traverser une importante épaisseur de résine, moins efficace sera le débullage naturel. Il peut être judicieux d’effectuer plusieurs coulées, ce qui permettra à la couche précédente de bien se dé-aérer.
Voilà pourquoi, il peut être éventuellement judicieux de privilégier un récipient plus large que haut.

NB: Le temps de repos disponible sera déterminé par le temps de vie en pot du mélange (“pot life ” en anglais). C’est à dire le temps durant lequel il est possible d’utiliser la résine (partie A et partie B) sans que ses propriétés ne soient modifiées. Pour simplifier, c’est le temps dont on dispose avant que le mélange de la partie A et B ne commence à durcir (ou polymériser). Il ne faut donc pas dépasser le temps de vie en pot de votre mélange car il ne sera plus possible de travailler votre résine (l’appliquer ou la couler). Certaines résines dégagent une forte chaleur (exotherme) et monte rapidement en température après le mélange. Ce type de résine présente des durées de vie en pot relativement courte. Cela signifie qu’il faut travailler, appliquer ou couler plus rapidement la résine.
RÉSINE ÉPOXY: QUELS RISQUES ?
Quels sont les risques liés à l’époxy ?
Quelles précautions faut-il prendre lorsque l’on travaille
avec ce type de résine thermodurcissable?
Beaucoup d’informations circulent sur Internet. Des rumeurs parfois inquiétantes, des
messages rédigés de façon approximative, sans source fiable, sans arguments scientifiques fondés, par des utilisateurs qui s’improvisent spécialistes. Aussi arrive
t-il que nous recevions des questionnements de la part de nos clients sur les éventuels risques qu’il y aurait à manipuler les résines époxy.
Nous nous proposons d’aborder ici tous les questionnements pour démystifier les croyances, apporter de vraies réponses à vos interrogations légitimes.
Pour commencer, les gens se méprennent souvent et confondent la résine époxy avec la résine polyester, composée de styrène (souvent plus de 30-40% selon le cas) et qui, elle, est très toxique et dont les émanations sont fort odorantes.
Ensuite, comme pour tout produit, il existe différentes qualités de résine époxy. Il n’est pas rare que l’on retrouve des solvants dans certaines résines vendues sur le marché.
Vous êtes en droit d’exiger de faire affaire avec des manufacturiers sérieux et exigeants qui sélectionnent chaque matière première, les analysent et les sélectionnent afin d’obtenir des systèmes thermodurcissables sans aucune matière ou composé organique volatile (COV ou VOC en anglais).
Des résines epoxy : 100 % COV
Il n’en demeure pas moins que la résine époxy est un produit chimique, qui, comme tout produit
chimique, requiert des précautions d’usages minimales, dont les premières relèvent du simple bon sens.
En plusieures ans d’expérience avec les résines thermodurcissables, nous n’avons jamais eu à déplorer aucun accident ou aucune problématique majeure que ce soit au sein de sa clientèle ou de son équipe.
En revanche, il est reconnu et avéré que les résines époxy sont une cause fréquente de dermatites ou d’eczéma de contact (allergies cutanées). La sensibilité ou la tolérance d’une personne à une autre étant sujet à de grandes variations, la meilleure prévention est donc d’éviter le contact et les éclaboussures.
NOS RECOMMANDATIONS :
-
Entreposage sécuritaire: entreposez les deux composantes, résine et durcisseur, hors de portée des enfants. (Ceci ne diffère nullement d’autres produits ménagers courants)
-
Pièce aérée : de préférence, évitez de travailler dans un milieu confiné. Favoriser un endroit correctement ventilé.
-
Protections minimales : le port de lunettes protectrices, de gants de type 4H, masque de protection respiratoire et tablier de rigueur.
-
Bien lire les fiches signalétiques des produits avant de les utiliser et suivre les directives au niveau de la protection.
* La directive européenne RoHS (2002/95/CE) vise à limiter l’utilisation de six substances dangereuses. En savoir davantage
Comment modifier la viscosité d’une résine thermodurcissable ?

Avant de savoir comment la viscosité d’une résine thermodurcissable peut être modifiée, voyons d’abord ce qu’est la viscosité et en quoi cela est important pour un utilisateur de résine thermodurcissable
Qu’est-ce que la viscosité d’une résine ?
La viscosité constitue une des principales caractéristiques typiques d’une résine ou d’un adhésif. Plus la viscosité est importante, plus le produit est épais. La capacité du fluide à s’écouler facilement diminue. Lorsque la viscosité est faible, le produit est davantage liquide ou fluide.
La viscosité se mesure en centipoise ou ” CP”, ce qui offre une échelle pour mesurer la viscosité d’une résine ou d’un adhésif.
- L’eau est à 1 CP
- Le miel à 2500 CPS
- Le beurre d’arachide à 200,000 CPS
Pourquoi la viscosité de la résine est un critère important ?
Voici pourquoi, il est bon de garder un oeil sur le paramètre de la viscosité:
- Pour appliquer un adhésif ou une résine
Les contraintes de travail ou la technique d’application peuvent largement influencer le choix d’un adhésif ou une résine. Ainsi, pour les applications verticales, on recommande des textures gel, ou versions plus thixotropiques pour éviter que le produit ne s’écoule sur la surface à recouvrir.
- Pour couler un moule
Par ailleurs, il peut être important de tenir compte de la viscosité de la résine lors de la fabrication d’un moule.
Prenons l’exemple d’un client qui a l’habitude de travailler avec un résine à base silicone pour fabriquer ses moules. Cherchant à augmenter la durée de vie de son moule, nous pouvons lui recommander un autre silicone présentant une meilleure résistance à l’élongation tout en conservant une dureté similaire (exemple : 30 de shore A) (Lisez ici notre article sur sujet de la dureté )
Cependant, quand on change de résine, il est préférable d’intégrer ce paramètre dans l’analyse. Si l’on a l’habitude de travailler avec une résine présentant une viscosité de 10, 000 cps, et que le nouveau produit utilisé a une viscosité de 50, 000 cps, les contraintes de travail peuvent être grandement affectées.
Travailler avec une résine plus épaisse, peut s’avérer problématique, notamment si le moule est particulièrement complexe. Une résine avec une plus haute viscosité pénétrera plus difficilement les recoins et interstices d’une matrice complexe, la circulation de la résine étant grandement diminuée.
-
Pour contrôler la formation de bulles
Sachez que plus une résine est épaisse, plus elle est difficile à débuller. A moins d’être équipé d’un autoclave, le risque avec une résine moins liquide est d’observer plus de bulles. Avec une résine plus liquide, le débullage naturel est facilité.
Qu’est-ce qui peut modifier la viscosité d’une résine ?
-
La température ambiante
Entreposée à une basse température, la viscosité de votre résine augmente (de même que le temps de vie en pot et les temps de démoulage et de polymérisation totale).
À l’inverse, au-delà de 22 degrés Celsius (72 degrès Fahrenheit), la viscosité baisse: la résine devient plus liquide (le temps de vie en pot diminue et le temps de cure est plus rapide).
Chaque 10 degrés F en moins ou en plus peut modifier de 50% les paramètres typiques d’un système thermodurcissable.
Dans un environnement de travail qui n’offre pas de conditions contrôlées, il ne fait donc pas de doute que travailler un produit en hiver ou en été peut être fort différent. En hiver, il peut arriver que l’on trouve sa résine plus épaisse….
-
L’ajout d’additif
Il est aussi arrivé qu’un client nous appelle pour savoir s’il était possible de “diluer” sa résine, en l’occurrence son silicone, pour qu’il soit moins épais.Il mentionnait en effet que le nouveau silicone qu’il avait récemment acheté était beaucoup plus épais que celui avec lequel il avait pris l’habitude de travailler .
Nous lui avons proposé d’essayer l’ajout d’un de nos produits, le Techno Fluide, à son mélange. Mais il s’agit la plutôt d’une solution de dépannage que nous ne saurions recommander d’adopter comme pratique.
En effet, il faut bien comprendre que tout agent de remplissage ou additif va nécessairement altérer les caractéristiques typiques et physiques de la résine. Ainsi cela peut modifier la viscosité, le temps de vie en pot, ou de cure, la résistance en tension, flexion, élongation…
Généralement, nous déconseillons de tenter de modifier les caractéristiques un produit par l’ajout d’additifs à moins que cela ne soit parfaitement contrôlé, par des tests préliminaires.
-
Ne jouez jamais avec le ratio de mélange
Mais surtout, l’idée de modifier la viscosité en abaissant ou augmentant la quantité de durcisseur dans un mélange est à proscrire. Le ratio de mélange préconisé doit impérativement être respecté. Tenter de le modifier nuirait à la réaction qui permet à la résine de catalyser en raison d’une stœchiométrie* déficiente
* résumé brièvement, la stœchiométrie correspond au calcul qui permet d’analyser les quantités de réactifs et de produits en jeu nécessaires à la parfaite réaction chimique qui produit une parfaite polymérisation de la résine. Autrement dit, le nombre de molécules de la partie A et de la partie B nécessaires pour une fermeture complète de la chaîne moléculaire.
Comment calculer la quantité de résine nécessaire à votre projet ?
Savez-vous calculer la quantité de résine dont vous avez besoin pour votre projet ? Combien de litres allez vous couler ? Quelle couvrance vous offre le kit de résine que vous venez d’acheter ?
Nous vous donnons ici les clés pour demeurer un acheteur prévoyant et éclairé.
I/ Calculer un volume de résine pour une coulée
1/ Trouver le volume en pouces cube ou en centimètres cubes
Vous devez vous assurer d’avoir les dimensions de votre moule dans une même unité
Longueur en pouces x largeur en pouces x hauteur en pouces = volume en pouces cubes
Longueur en cm x largeur en cm x hauteur en cm = volume en centimètres cubes
2/ Trouver le nombre de litres que peut contenir ce volume
Volume en pouces cubes x 16.38 ml /1000 = nombre de litres
*NB: 1 pouce cube = 16.38 ml
Volume en centimètres cubes /1000 = nombre de litres
Pensez ajouter 3% pour les pertes
II/ Calculer une couvrance de résine pour une application en couche mince
1/ Trouver la quantité en millilitres du kit que vous vous apprêtez à acheter
Si la contenance du kit de résine est annoncé au poids, vous avez besoin de connaitre la
densité spécifique du produit.
Exemple: un kit de résine de CRYSTAL CLEAR 12 kg dont la densité spécifique est de 1.08.
Ce kit contient 12/ 1.08 = 11.111 litres soit 1111 millilitres
Les 8 raisons pour lesquelles un sol époxy peut échouer
Les revêtements époxy sont des matériaux fantastiques qui vous permettent de créer de grandes surfaces totalement continues, sans avoir à projeter de joints sur elles. Ce type de revêtement de sol est une protection de surface idéale pour de multiples domaines d'application, qu'il s'agisse de locaux commerciaux, de parkings ou de zones industrielles exigeant des performances élevées.
Les chaussées en résine offrent de grands avantages et améliorations par rapport à un support de base en ciment traditionnel. Ils augmentent considérablement leurs performances mécaniques, chimiques et esthétiques devant un éventail diversifié de sollicitations auxquelles ils peuvent être exposés.
De nombreux facteurs peuvent créer des affections au moment de l'installation d'un sol en résine époxy continue. Contrairement à d'autres secteurs, dont la fabrication de leurs produits peut être soumise à des environnements totalement contrôlés au niveau environnemental, humidité, température et même tous ces éléments qui pourraient avoir un impact sur eux, la pose de chaussées en résine constitue un processus complexe , manuel, avec de nombreuses variables dans l'équation qui peuvent interférer chimiquement avec les matériaux utilisés qui échappent souvent au contrôle complet de l'installateur. Pour cette raison, faire un bon choix d'un installateur qualifié possédant une vaste expérience dans ce domaine est crucial, avec des critères suffisants,
En tant que professionnels dans ce domaine, nous savons que tous les sols ne sont malheureusement pas de bons candidats pour un sol époxy, et nous en trouvons tous les jours avec toutes sortes de situations. Qu'il s'agisse d'environnements d'application défavorables, de supports peu compétents ou fortement contaminés, de temps d'installation extrêmement limités qui nécessitent également une mise en service rapide et des performances optimales, ce qui nécessite l'utilisation continue de solutions ad-hoc.
Les 8 raisons pour lesquelles un sol époxy peut échoue1. Mauvaise préparation de la surface d'appui
Avant d'appliquer la couche d'apprêt, il est nécessaire de réaliser le poncage approprié pour obtenir une pénétration élevée et ainsi obtenir un bon ancrage capable de fixer le nouveau produit avec le sol existant. Il est essentiel d'ouvrir les pores et de nettoyer le support pour obtenir un collage correct. La surface doit toujours être propre, sèche et exempte de poussière, d'huile, de graisse ou de tout autre contaminant.

2. Humidité
Les systèmes époxy à base de solvant ne lient pas correctement les supports humides ou humides. Il est important de s'assurer que la surface est complètement sèche et qu'il n'y a pas de remontée ou d'humidité résiduelle du support lui-même. Les méthodes de détection actuelles sont mises en œuvre à l'aide d'équipements de mesure, bien que moins fréquemment, des membranes étanches soient également utilisées comme test de détection d'humidité à plusieurs endroits aléatoires de l'installation.
Malgré cela, toutes les humidités ne se manifestent pas de façon permanente car il existe différents types d'humidité. Les humidités peuvent être à l'origine de graves problèmes, avec des manifestations intermittentes, entraînant une perte de solidité du support ainsi que de fortes pressions ascendantes dues à la capillarité conduisant à la perte de revêtements polymères.
Ces types de problèmes sont causés par plusieurs raisons, dont la gravité des dommages dépend de plusieurs facteurs, soit dans des zones spécifiques en raison de la rupture des installations d'eau conductrices sous la chaussée, soit principalement en raison de l'accumulation de fuites d'eau contenues dans le sous-sol. Normalement, c'est le niveau phréatique de la zone qui génère la saturation du sol par les eaux pluviales qui n'a pas à évacuer, mais si en plus de ce paramètre on ajoute des temps très pluvieux la situation s'aggrave généralement, et plus rapidement si la montée en eau Il transporte de nombreux minéraux du sol. Pour cette raison, un bon conseil pour prévenir les pathologies causées par l'humidité est d'avoir une bonne isolation entre le sol et le support qui agit comme une barrière contre la vapeur d'eau .

3. Un support faible
Il s'agit d'un problème courant causé par une chaussée de mauvaise qualité pour diverses raisons; Chaussées épuisées qui ont pratiquement rempli leur tâche (dépassant largement les cycles de chargement pour lesquels elles ont été conçues), une faible teneur en ciment ou un excès d'eau dans le mélange. Ce dernier réduit la résistance caractéristique du béton provoquant un déséquilibre dans le rapport eau-ciment, ce qui fait que la chaussée époxy est plus résistante que le substrat et sa propre traction se soulève provoquant son détachement et même avec une partie de la support qui lui est attaché.

4. N'utilisez pas d'apprêt ou utilisez un apprêt incorrect
Juste après avoir préparé le substrat, l'apprêt approprié doit toujours être appliqué et son temps de séchage doit être respecté pour assurer une bonne adhérence avec le système époxy. En ce sens, une fois l'apprêt sec, la pose de la chaussée ne doit pas être retardée. Dans ce cas, un ponçage de surface doit être effectué avant l'application du système pour assurer une bonne adhérence. Le revêtement d'un support céramique nécessite un apprêt céramique. La même chose se produit si le support est en béton ou si le support est en métal. Chaque support correspond à son amorce.

5. Surface incompatible
Il est essentiel de s'assurer que la surface est compatible avec les revêtements de sol époxy, tant du point de vue de l'adhérence que de la résistance à la traction.
Par exemple, il n'est pas recommandé d'appliquer un revêtement époxy directement sur une surface de méthacrylate de méthyle sans un sablage intermédiaire complet, ou des matériaux époxy rigides ne doivent pas être utilisés sur des substrats en bois standard. Le bois naturel est beaucoup plus flexible que l'époxy et provoquera la fissuration du revêtement car l'époxy n'a pas de dilatation du bois. Dans ce cas spécifique, il est préférable d'utiliser des panneaux DM hydrofuges qui peuvent être revêtus de matériaux époxy, et si possible avec des matériaux avec un module élastique plus élevé, tels que les polyuréthanes.
6. Sols contaminés
Ces problèmes sont plus courants dans le remodelage des installations qui doivent reconditionner leurs anciennes chaussées. Des activités industrielles ont déjà été menées sur ces supports, qui au fil du temps ont absorbé les contaminants capillaires tels que les huiles, les graisses ou autres résidus qui peuvent provoquer un mauvais ancrage de la chaussée dans ces zones spécifiques et même dans celles-ci le revêtement se détache. Pour cette raison, si la contamination est superficielle, il existe des méthodes de décontamination efficaces telles que l'utilisation de produits chimiques de décontamination ou de préparations de support plus intensives, entre autres. Mais si le degré de contamination est très élevé, les options sont considérablement réduites.
Malheureusement, les industries sont encore peu conscientes du fait que des niveaux élevés de pollution peuvent entraver considérablement l'installation future de systèmes de pavage en polymère, et une fois que le support est contaminé en profondeur, il est extrêmement difficile de le décontaminer et même à de nombreuses reprises, il est tout simplement impossible. Heureusement, dans ce sens au cours de ces dernières années, il y a eu un changement de mentalité important dans les industries, et la tendance dénote une priorité des environnements de travail propres et sûrs qui contribuent à promouvoir la productivité, sans oublier un engagement ferme envers la durabilité et le soin et le respect de l'environnement.
D'un autre côté, la pollution n'affecte pas seulement le substrat. Dans le jargon des installateurs professionnels de sols, nous appelons non seulement des éléments de «pollution» qui s'élèvent du support au revêtement, et même ceux-ci ne doivent pas nécessairement polluer l'environnement. En fait, nous nous référons à tout élément qui a la capacité de créer une quelconque affectation aux matériaux que nous utilisons pour fabriquer la chaussée, et surtout, lors de son installation et de son séchage. Il y a souvent des contaminants qui font partie des intrants de la chaîne de production du client, tels que des matériaux volatils qui sont en suspension dans l'environnement et peuvent produire des altérations (plus visibles lorsque les textures de finition sont plus lisses), bien que dans ce sens habituellement

7. Mélanges de résines défectueux
Durcissement incorrect, adhésivité prolongée ou état de sécheresse au toucher ou " prise " longtemps après que le matériau ait séché. Cela peut être dû à l'utilisation de mélanges avec des composants dans des proportions incorrectes ou dans des temps de mélange insuffisants. En ce sens, les instructions du fabricant doivent toujours être strictement suivies pour obtenir un bon résultat avec chaque mélange et garantir leur homogénéité tout au long de l'application. Cela permet de contrôler parfaitement les temps de séchage entre les couches afin de réduire les risques de problèmes.
8. L'utilisation de la surface avant qu'elle ait durci chimiquement
Bien qu'il existe actuellement des matériaux permettant d'accélérer les temps de séchage, il est habituel qu'en raison des besoins de l'installation elle-même, sa mise en service ne puisse pas être retardée plus d'un jour ou deux au plus après la fin de la chaussée.
Lorsque le besoin est impératif et que le revêtement de sol nouvellement installé doit être entretenu de manière imminente et qu'il est inévitable de ne pas pouvoir respecter le temps de séchage complet, il n'y a plus rien à dire, mais il est toujours conseillé, dans les cas où cela est possible, de respecter une temps de séchage plus long
Il est souvent évident que les revêtements époxy conventionnels prennent 7 jours pour durcir chimiquement, et même pour atteindre une adhérence totale à la surface. Cela ne signifie pas que vous ne pouvez même pas marcher dessus après plusieurs jours. Cela signifie que, dans la mesure du possible, le contact avec l'eau, un nettoyage très intensif ou l'utilisation de machines lourdes est reporté de quelques jours de plus jusqu'à ce que le revêtement de sol époxy ait complètement durci chimiquement.
PRÉPARATION DE SURFACE POUR L'APPLICATION DU EPOXY
1. PRÉPARATION DE SURFACE POUR L'APPLICATION D'UN RM La préparation du sol avant l’application d’un revêtement, est une étape essentielle qui détermine la qualité et la bonne tenue dans le temps de l’ouvrage réalisé. Cette opération doit être effectuée dans la règle de l’art, soit par grenaillage soit par ponçage des supports..

Le Ponçage Le ponçage permet d’éliminer les anciens revêtements tout en rectifiant la planéité des supports. Les surfaces traitées, permettent l’adhérence de tous les systèmes de recouvrement ultérieurs (résine, sols souples…). L’opération de ponçage permet de traiter en totalité, les périphéries de sol, au droit et aux angles des murs, en une seule opération et représente donc une économie de temps, de produit et donc d’argent. Une préparation soignée des surfaces est incontournable pour assurer esthétique et durabilité du revêtement appliqué. Le ponçage rend la surface uniforme et homogène. La préparation d’un sol par ponçage peut ensuite être suivie d’un polissage ou d’un bouchardage de surface.

Dans cet article, nous allons couvrir tous les aspects importants dans la préparation de surface qui recevra un RM. Nous disons toujours que la préparation de surface est le «fondement» du revêtement haute performance et, pour cette raison, il doit être très bien fait. Il n'y a aucun avantage à réaliser un revêtement avec d'excellents produits, une épaisseur élevée si la préparation est mal faite et en quelques mois le revêtement commence à se démarquer. Pour réussir la préparation de surface, vous devez observer un certain nombre d'éléments qui sont souvent négligés. La première chose à noter est la suivante: Est-ce que ce substrat sera enduit ont les exigences de résistance minimum à revêtir? Ce n'est pas n'importe quel substrat (béton, mortier, céramique, pierre, etc.) qui peut être recouvert, si le substrat n'a pas de résistance minimale à la traction, à la compression, à la porosité et à l'intégrité. 2. RÉSISTANCE AU TRACTION Techniquement, selon l'ICRI (International Concrete Repairs Institute), un support doit avoir au moins 1,4MPa de résistance à la traction ou 100% de cohésion dans le matériau du chariot (voir photo)

Ce test est précis mais il nécessite du temps et de l'équipement et, en pratique, il n'est exécuté que lorsque l'on a vraiment des doutes sur la résistance du béton. Un processus d'enquête plus simple peut être fait avant que cet essai soit terminé. Un test très simple peut être fait avec un outil pointu tel qu'un clou ou un boulon ou une clé forte. Avec cet outil, il frotte lourdement sur le sol, en vérifiant si le sol résiste aux rayures ou non. Si elle ne résiste pas, il y a une forte indication que la surface du substrat ou le substrat entier n'a pas la résistance minimale à revêtir. Voir les photos:

3. RÉSISTANCE À LA COMPRESSION Un autre processus d'investigation pour déterminer si un support peut ou non être recouvert est l'utilisation du scléromètre. Aucun support ne doit être recouvert si la résistance aux chocs est inférieure à 25 MPa. Normalement, lorsqu'un revêtement ne mesure pas au moins 25 MPa, il laisse une marque sur le substrat. Voir les photos:

4. POROSITÉ Une fois qu'il est déterminé que le substrat a une résistance minimale à revêtir, nous devons maintenant déterminer sa porosité. Pour notre intérêt dans la préparation de surface, l'adhérence du revêtement au support, nous pouvons définir la porosité comme la capacité d'un support à absorber ou non un liquide (résine époxy, polyuréthane, uréthane, etc.) à appliquer sur le support La porosité a beaucoup à voir avec la structure du support, qu'il y ait beaucoup de vides ou qu'il soit bien collé et qu'il ait une relation directe avec la résistance du substrat, la finition de surface donnée au substrat et les contaminations de surface possibles comme cires ont été appliqués, la vieille peinture, le processus de ponçage, etc. Si la surface est trop "fermée", soit parce que le substrat est bien collé, soit parce que la surface est "fermée" par une finition hautement vitrée avec application de durcisseurs de surface, soit par un processus de talochage, c'est certainement plus il faut être très prudent car si une préparation de surface appropriée n'est pas faite, l'ouverture de cette porosité, permettant à la résine de pénétrer et d'adhérer au substrat, tout le revêtement ca va décoller et le le revêtement sera perdu. D'autre part, si une surface est très poreuse, elle est toujours mate, généralement légère, elle absorbe beaucoup de résine pendant l'application, ce qui indique qu'il y a beaucoup de vides dans sa structure et indique qu'elle a une faible résistance à la traction et compression . Un autre problème sérieux avec les surfaces très poreuses est qu'elles consomment beaucoup de résine sans générer d'épaisseur sur le revêtement, causant des dommages à l'applicateur et au client final. L'idéal est une surface avec une porosité intermédiaire, qui a la force mais absorbe en même temps la résine appliquée. Un moyen simple de déterminer si une surface est poreuse ou non est un test d'eau. Un peu d'eau est appliquée à la surface et après 30 secondes on observe si l'eau a été absorbée (très poreuse), non absorbée (très fermée) ou plus sombre mais pas totalement absorbée (idéal).
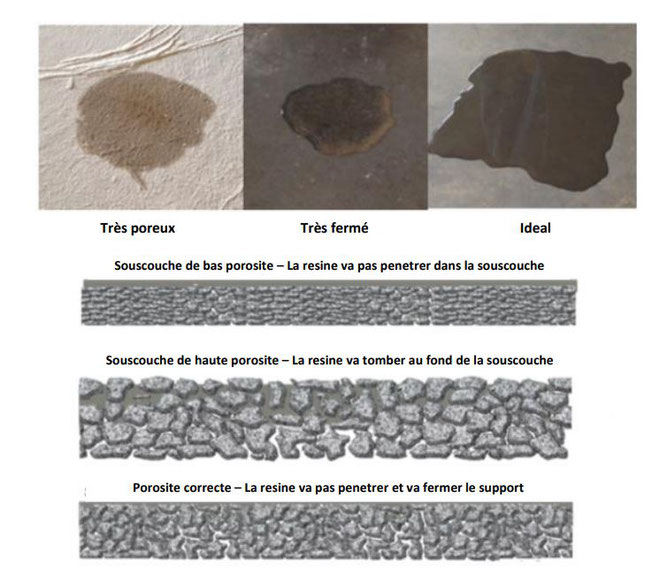
5. INTÉGRITÉ Quand nous disons qu'un substrat doit être intact, nous voulons dire qu'il est structurellement adéquat et qu'il n'a aucune contamination, qu'il s'agisse d'huile, de graisse, de paraffine, de silicone, de vieille peinture, de saleté en général, etc. Si le support est structurellement compromis (voir photo), il n'y a rien à faire, il n'y a pas de revêtement qui puisse surmonter ces défauts, donc le substrat doit être enlevé et redécoupé.

Si le support présente des contaminations dépendant de la sévérité et de la profondeur, il peut être recouvert, mais ceci fera l'objet d'un autre article. Une fois qu'il est déterminé qu'un substrat a toutes les conditions à revêtir, nous devons maintenant définir quel type de préparation de surface doit être fait pour s'adapter au revêtement et au substrat. 6. TEXTURE DU SUBSTRAT - CSP L'ICRI a créé il y a quelques années une norme de profil de plancher en béton appelée profil de surface en béton CSP ( Concrete Surface Profile). Avec ce modèle, nous pouvons déterminer deux caractéristiques importantes, la texture du substrat à revêtir et la texture du substrat après la préparation de la surface. Ce motif est très important car il aide et définit quel revêtement est le plus adapté à la texture du substrat à revêtir et quel équipement doit être utilisé pour obtenir un CSP particulier nécessaire pour une épaisseur de revêtement donnée.


Après la largeur et la longueur de la zone à revêtir, la préparation de surface est la «troisième dimension» est la profondeur et est la seule qui peut être déterminée par le technicien du revêtement. Les techniques de préparation de surface les plus courantes sur le marché suivent deux principes: abrasion (polissage, meulage, ponçage) et impact ou projection (fraiseuses, meuleuses, Type revetement Sellement/ Peinture 150-300µm marteaux, etc.) Les équipements de préparation qui utilisent le principe d'abrasion génèrent généralement CSPs plus bas, généralement CSPs 1, 2 maximum 3. Un équipement de préparation utilisant le principe de l'impact ou de la projection donne généralement des CSP plus élevés, typiquement CSP 3 à 9. Ces principes vous aident à choisir le meilleur équipement parce que si votre plancher a un CSP 5 et que vous voulez peindre sur le plancher, vous devrez obtenir un plancher avec CSP 2, ainsi vous devriez employer une machine de polissage pour réduire CSP 5 à 2. L'inverse est également vrai. La corrélation entre les types d'équipements et les CSP pouvant être obtenus avec chacun d'eux peut être consultée sur le site internet de l'ANAPRE dans la section Technical Recommendations - ANAPRE CR 004/2012. 7. RÉSUMÉ 1- Une surface qui n'a pas de résistance minimale ne doit pas être rercouverte et ne doit donc pas être préparée. 2- Une surface doit avoir un minimum de 1,4 MPa de résistance à la traction et 25MPa de résistance à la compression. 3- Deux variables déterminent l'adhérence du revêtement au substrat, la porosité et la zone d'adhésion. Aucune porosité, même si elle a une zone d'adhérence, le revêtement n'adhère pas. Avec une porosité mais pas de surface, l'adhérence peut être insuffisante. Le CSP peut être du substrat ou du type de préparation choisi. La préparation définira les 3 dimensions dans la zone de contact. 5- Le CSP du substrat peut déterminer quelle épaisseur de revêtement doit être appliquée. 6- Le choix du type d'équipement de préparation de surface et par conséquent du CSP de la préparation est fonction de l'épaisseur du revêtement qui sera appliqué. 7- Pour diminuer le CSP d'un support, utiliser un équipement abrasif (ponçage). Pour augmenter le CSP d'un support, utilisez un équipement d'impact ou de projection (routeur ou dynamitage).